Product recalls and safety issues can have significant implications for pet food manufacturers, not only in terms of financial costs but also reputation and consumer trust. Proactive management of these situations is crucial to protect both the well-being of pets and the brand integrity of manufacturers. In today’s fast-paced world, where information spreads quickly, it is essential for pet food manufacturers to have robust protocols in place to address product recalls and safety issues swiftly and effectively. This article will outline the key protocols that pet food manufacturers in the USA should have in place to manage dog food recalls, with a focus on dog food recalls today and the broader landscape of dog food recalls.
Table of Contents
Rapid Identification And Investigation:
The first step in addressing product recalls or safety issues is rapid identification and investigation. Pet food manufacturers should establish a process for monitoring and reviewing reports from consumers, veterinarians, regulatory agencies, and internal quality control systems. Timely identification of potential issues allows manufacturers to initiate investigations promptly to determine the cause, scope, and severity of the problem. Collaborating with experts and conducting thorough root cause analyses helps identify the source of the issue and inform subsequent actions.
Clear Communication Plan:
Effective communication is paramount during product recalls and safety issues. Manufacturers should have a comprehensive communication plan in place to ensure transparency and timely dissemination of information. This includes developing clear and concise messaging for internal teams, stakeholders, retailers, consumers, and the media. Communication channels, such as websites, social media platforms, and customer service lines, should be readily accessible for pet owners seeking information or assistance. Maintaining open lines of communication helps manage expectations and address concerns in a timely manner.
Swift Action And Corrective Measures:
Once the issue and its root cause have been identified, pet food manufacturers must take swift action and implement appropriate corrective measures. This may involve halting production, initiating product recalls, and implementing changes to manufacturing processes, ingredients, or formulations to rectify the problem. Manufacturers should work closely with regulatory agencies to ensure compliance with applicable regulations and guidelines. Instituting internal controls and monitoring systems helps prevent recurrence and provides assurance of ongoing product safety.
Collaboration With Regulatory Agencies:
Collaboration with regulatory agencies is essential during product recalls and safety issues. Pet food manufacturers should establish relationships with relevant regulatory bodies, such as the Food and Drug Administration (FDA) in the USA, to facilitate information exchange and coordinate actions. Promptly notifying regulatory agencies about potential issues demonstrates commitment to consumer safety and compliance. Collaboration with regulators also helps ensure that manufacturers are informed about current regulations and industry best practices to prevent future safety concerns.
Comprehensive Recall Management:
Pet food manufacturers should have a comprehensive recall management plan in place to guide the execution of product recalls effectively. This plan should include detailed procedures for recall initiation, logistics, communication, and documentation. Manufacturers must identify key stakeholders involved in the recall process, establish recall teams, and define their roles and responsibilities. Regular mock recall exercises and drills help test the effectiveness of the recall management plan and ensure preparedness in case of an actual recall.
Continuous Improvement And Lessons Learned:
Product recalls and safety issues provide valuable opportunities for pet food manufacturers to learn and improve their processes. Manufacturers should conduct thorough post-recall analyses to identify areas for improvement in quality control, ingredient sourcing, production, and communication. Implementing corrective actions based on the lessons learned helps prevent similar issues from occurring in the future. Regular reviews and updates to protocols and procedures ensure that manufacturers stay proactive in addressing emerging safety concerns.
In Conclusion
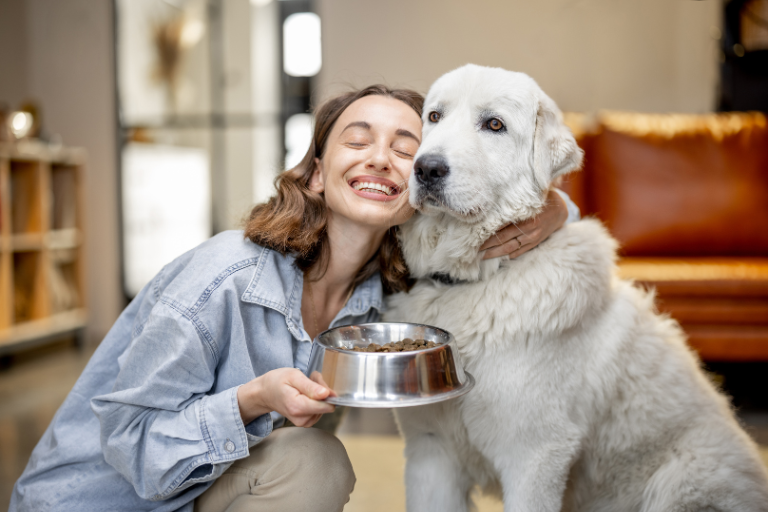
Having well-defined protocols in place to address product recalls and safety issues is crucial for pet food manufacturers. By swiftly identifying and investigating potential issues, maintaining clear communication, taking swift action and implementing corrective measures, collaborating with regulatory agencies, executing comprehensive recall management plans, and embracing continuous improvement, manufacturers can effectively manage dog food recalls today and safeguard the well-being of pets. These protocols not only protect consumers but also preserve the reputation and trust of pet food manufacturers in the USA.